Academic Profile - Dr Rob Innes
Innovations in sustainable tyre recycling
Dr (James) Rob Innes is a Post-Doctoral Research Associate at the University of Bradford's Polymer IRC investigating the processing of difficult to recycle polymers and elastomers, with a particular interest in tyres. Here he talks about his career journey so far, the challenges of tyre recycling and why it's important that we address the issue of tyre waste...
Can you tell us about your background?
I did Chemistry at the University of Manchester, which I picked as a degree subject because I had a great Chemistry teacher at school and it just seemed really interesting. The degree was great, and in the last year there was one project I particularly enjoyed. I did really well on it, and my professor told me about a PhD opportunity which was very similar to the work I’d done and encouraged me to apply. This made me think maybe I should also apply for another PhD, which was on graphene in rubber jointly part of the BP International Centre for Advanced Materials and the National Graphene Institute at the University of Manchester, and this is the one I ended up doing. It was a Centre for Doctoral Training programme so I did a year as a master's crossover and then three years of actual research on putting graphene in rubber, focusing on seals for oil and gas. We got really good results and there's still companies that contact me about opportunities involving graphene based on my thesis.
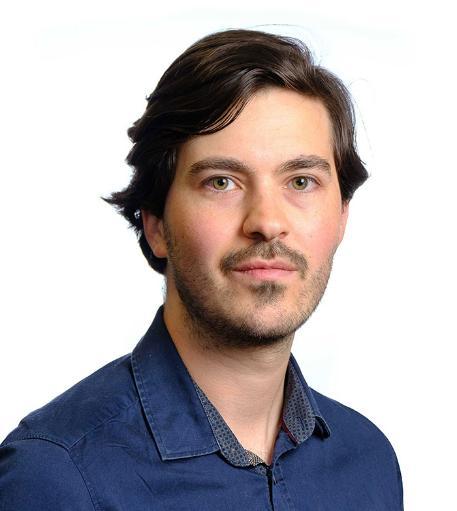
Dr Rob Innes
Why did you choose to move to the University of Bradford?
When this was coming to an end, I started looking for other opportunities and came across the low carbon recycling grant project at Bradford - I thought the recycling of polymers sounded fascinating, and Prof Phil Coates did a good job of convincing me that this was the right role for me.
This was 2019, and we were looking at recycling mixed waste streams, in collaboration with Sichuan University in China. Originally the plan was that we would have lots of research exchanges where we'd be trying to help them improve their technology. Unfortunately, COVID happened and the opportunity to fly to China was gone, so we only managed to visit once in 2019. Plan B was getting equipment sent over from China to continue the work, and we were looking at different things you could do with mixed waste, including ground tyre rubber, which I ended up focusing on more and more. When I realised how large the volume of tyres was and how valuable tyres are, I knew this was an important area of research.
Tell us about your research into tyre recycling...
Recycling tyres is very difficult as they are very complex products – there are four different components that make up a tyre: the carcass, the sidewall, the steel and fabric reinforcing, and the tread. There can be more than 100 ingredients that go into a tyre, and you can’t just melt it down like with plastics.
We want to improve the research so that we can get it to a stage where tyres can be recycled as new tyres, rather than low value applications like playground filler. Currently it’s estimated that a maximum of 20% recycled rubber could go into a tyre, however most products don’t contain any recycled rubber. We’d like to increase both the upper limit, to between 30-50%, and the actual amount of recycled rubber used by manufacturers.
Our recent RIEDA (Research, Innovation and Engagement Development Account)-funded project was looking at the characteristics of a tyre tread with no recycled material, and how the chemistry and structure changes as we break it down. We then put in recycled material and tweaked the chemistry to match these properties.
We had limited time and scope, so we just did one test at 23% recycled material, but we did it across nine different versions to look at different parts of the science across all the known formulations. We got the same mechanical properties including tensile strength which was a really important result, and now there are a lot of companies that are interested in the work, including Pirelli, who said they'd be happy to be a mentor for the UKRI Future Leaders Fellowship bid that I’m preparing to submit for.
We've now built about 15 project partners offering about £1 million of support with a £2 million government bid, so the next stage would be a potential £3 million project if successful. We want to work with partner companies to establish what their recycling technologies produce in the chemistry and structure of the rubber, focusing on what technologies already exist on an industrial scale, and how we can make them work better.
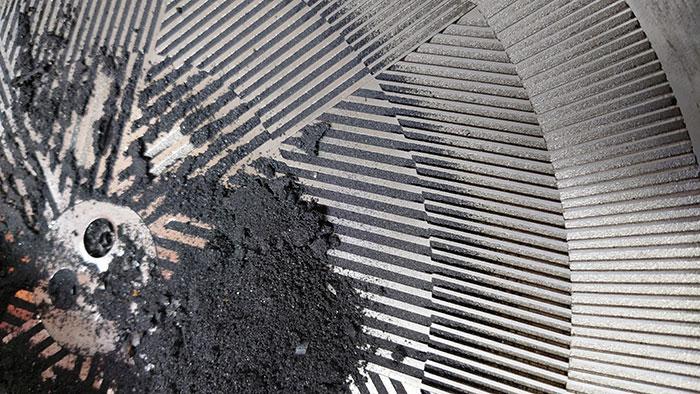
Solid-state shear milling equipment with ground tyre rubber.
Why is it important to take a more sustainable approach to tyre production and recycling?
Natural rubber is harvested from one tree species, Hevea Brasiliensis, grown in South and South East Asia, and there are some ethical and environmental concerns over the deforestation that’s taken place to make room for these plantations. There’s also the fact that as this is a single species, there is the possibility that disease could wipe out the entire population of trees, which would cause a crisis for the rubber industry. This is why reducing the quantity of natural rubber in each product is desirable, especially as tyres make up 70% of all rubber products. On top of this there's also synthetic rubber in tyres, which is derived from oil, where there are obvious environmental and cost benefits to replacing this with recycled rubber.
Tyre waste is also a huge environmental issue as 1.5 billion waste tyres are generated every year (as I discussed in my article for The Conversation) and many of the UK’s used tyres are shipped to places like India, where they are burned for energy/oil in a way that releases toxic pollutants which are extremely harmful to the environment, especially for the local area and its inhabitants.
Can you tell us about your recent engagement activities, and what’s coming up for you?
I recently did a Pint of Science talk (informal lectures aimed at a non-scientific audience) where I talked about what happens to your tyre when it gets collected at the garage. I asked the audience questions like ‘what does recycling mean to you?’, and ‘What percentage of car passenger tyres were retreaded in the UK last year?’ (the answer is zero). It was interesting to gauge what people thought about the subject and I enjoyed speaking to a different type of audience.
I also went to the European Tyre Recycling Association Conference in Brussels recently, which opened my eyes to forthcoming EU regulations that will have a significant impact for the rubber industry.
In terms of what’s coming up, I’m hoping to do more testing to push the findings of the RIEDA project further and to get more recycled product into the tyres, and I’m also involved in a project looking at recycling polypropylene and polyethylene waste.
And thinking of engagement, I’d love to raise the profile of recycled tyres by making a video featuring some world class rally drivers racing with recycled tyres on their cars and seeing what they thought. That’s a few years away though, and dependent on funding, but fingers crossed...
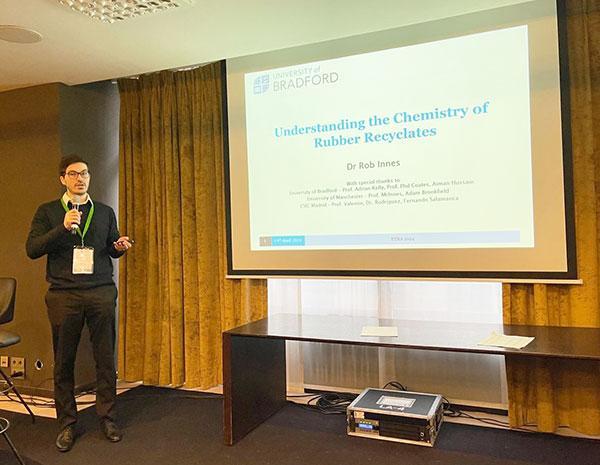
Rob Innes presenting his research at the European Tyre Recycling Association Conference, April 2024