Academic Profile - Dr Kavian Cooke
Collaborating with industry to create innovative materials
Dr Kavian Cooke, Associate Professor in Material Science and Engineering and Director of Postgraduate Research, joined the University of Bradford in 2017. Here's he talks about his career journey and research interests that include tribology (how moving surfaces interact, including friction, lubrication, and wear), material science and surface engineering...
Can you tell us about your background, and how your research interests developed?
Hailing from Jamaica, a nation with a rich engineering heritage, my initial academic journey was focused on engineering. However, during my undergraduate studies at the University of Technology, Jamaica, a burgeoning interest in research eclipsed my aspirations for a purely engineering career.
My final-year BEng project, undertaken in collaboration with the Sugar Industry Research Institute (SIRI), marked a pivotal moment. I worked on the development of a coating to mitigate wear on sugar cane milling machine components, which proved highly successful, culminating in two publications and a scholarship to pursue a Master's degree in Tribology. Following this, my academic career developed at the University of Technology, Jamaica with Assistant Lectureship and Lectureship roles.
Subsequently, a scholarship to the University of Calgary enabled me to undertake a PhD in Engineering under the supervision of Professor Tahir Khan, focusing on the diffusion bonding of aluminium alloys for aerospace applications.
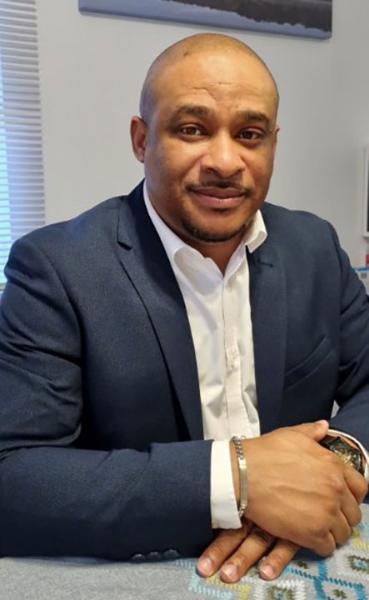
Dr Kavian Cooke
While my research has broadened to encompass materials science and additive manufacturing, my core interest in diffusion bonding (using high pressure and high temperatures create to an undetectable bond between two surfaces) persists. I have delved into joining advanced alloys using nanocomposite coatings, with a particular emphasis on applying this technique to aerospace materials. The inclusion of nanosize particles within the weld has significantly enhanced the efficiency of the process, and this approach won me the University of Technology Award for Excellence in Research in 2013.
A subsequent role as Head of the Mechanical Engineering department at the University of Technology, Jamaica, led to a fortuitous reunion with Professor Khan. His invitation to join his research team at the University of Bradford marked a turning point, introducing me to the field of additive manufacturing for wear and corrosion-resistant coatings. Since joining the university in 2017, I have progressed to the role of Associate Professor and Director of Postgraduate Research within the Faculty of Engineering and Digital Technologies.
Can you describe your research focus at the University of Bradford?
Our research approach at the University of Bradford distinguishes itself through a strong emphasis on industry collaboration. Rather than confining our efforts to fundamental science, we actively seek real-world applications for our research findings. This allows us to refine our laboratory-based work in response to industrial challenges, ultimately delivering more effective solutions.
My research primarily spans materials science and engineering, with a particular focus on surface engineering and tribology. I employ a diverse range of methodologies to design materials capable of enduring extreme conditions, such as high temperatures, heavy loads, and corrosive environments.
A key component of our work involves partnering with small and medium-sized enterprises (SMEs) to leverage advanced techniques and equipment tailored to their needs. Our goal is to enhance their efficiency and facilitate the development of innovative products. The SIBLING project, for instance, saw the acquisition of a cutting-edge JEOL field emission scanning electron microscope (SEM), enabling detailed analysis of material composition, crystallographic structure, and the impact of physical and thermal changes on material behaviour.
Our research has led to the development of novel coatings that enhance the diffusion bonding of aluminium alloys through an electroplating process. This technique holds the potential for industrial application as a self-contained, accelerated additive manufacturing process akin to 3D printing. We are also developing coatings that respond to environmental changes and protect materials from corrosion and wear, as exemplified by a recent project that yielded a nanocomposite coating capable of quadrupling the surface lifespan of metals.
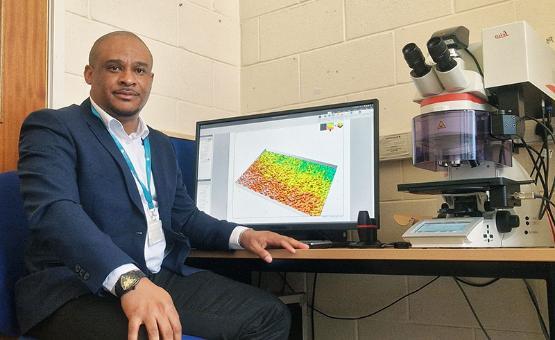
Dr Kavian Cooke demonstrating the electrochemical corrosion testing of materials.
Are there any other current and upcoming projects you'd like to mention?
In addition to materials development, we are engaged in projects such as Fab2Paper, which transforms waste fabric into high-quality paper, and an Innovate UK-funded study investigating the potential of fabricating high-quality paper from waste fabric. Furthermore, a collaborative project with colleagues in Pharmacy and Computer Science, funded by Brad-Attain PhD Studentship, aims to develop additive-manufactured stainless steel materials for implantable medical devices.
Building upon the success of the SIBLING and CAYMAN projects, we are committed to expanding our engagement with local SMEs. This aligns with the Faculty of Engineering and Digital Technologies' vision of establishing a Manufacturing Institute to foster stronger ties with industry and solidify our position as a leading centre of excellence in materials science and engineering.