KTP project examples
Knowledge Transfer Partnership - Fighting diseases using bee ‘propolis’
Nature’s Laboratory Ltd, a natural medicine producer in Whitby, have been working with the University of Bradford’s Centre for Pharmaceutical Engineering Science on a Knowledge Transfer Partnership to characterise and quantify the compounds of propolis in different bee colonies around the world - part of their BeePharma Africa Project … Local Help for Local Health.
Anant Paradkar, Professor of Pharmaceutical Engineering at the University of Bradford, has been working with the company on propolis related research for over ten years, including a previous Knowledge Transfer Partnership.
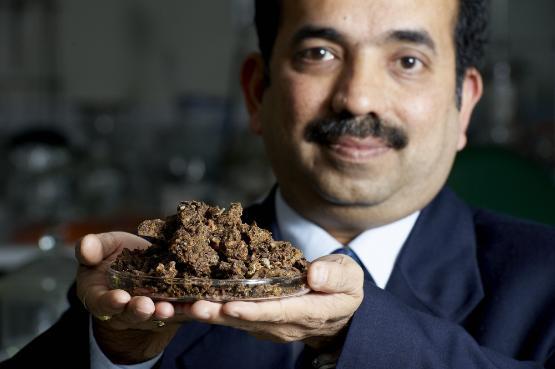
Knowledge Transfer Partnership project transforms food company into technology driven enterprise
Dr Savas Konur, Lecturer in Computer Science, worked with Rakusens Ltd, a Leeds based kosher food manufacturer, on a Knowledge Transfer Partnership (KTP). The project, rated outstanding by Innovate UK, transformed production knowledge into a smart manufacturing process using Artificial Intelligence, Machine Learning, Big Data, Cloud Computing and Industrial Internet of Things to produce consistent quality food products.
The company, a very traditional business with a long and cherished history, was experiencing large variations in product quality, taste and texture. Product lines were technically identical but switching products between lines created inconsistencies, making it impossible to have a flexible planning process that allowed the company to reach its ‘real’ capacity opportunity.
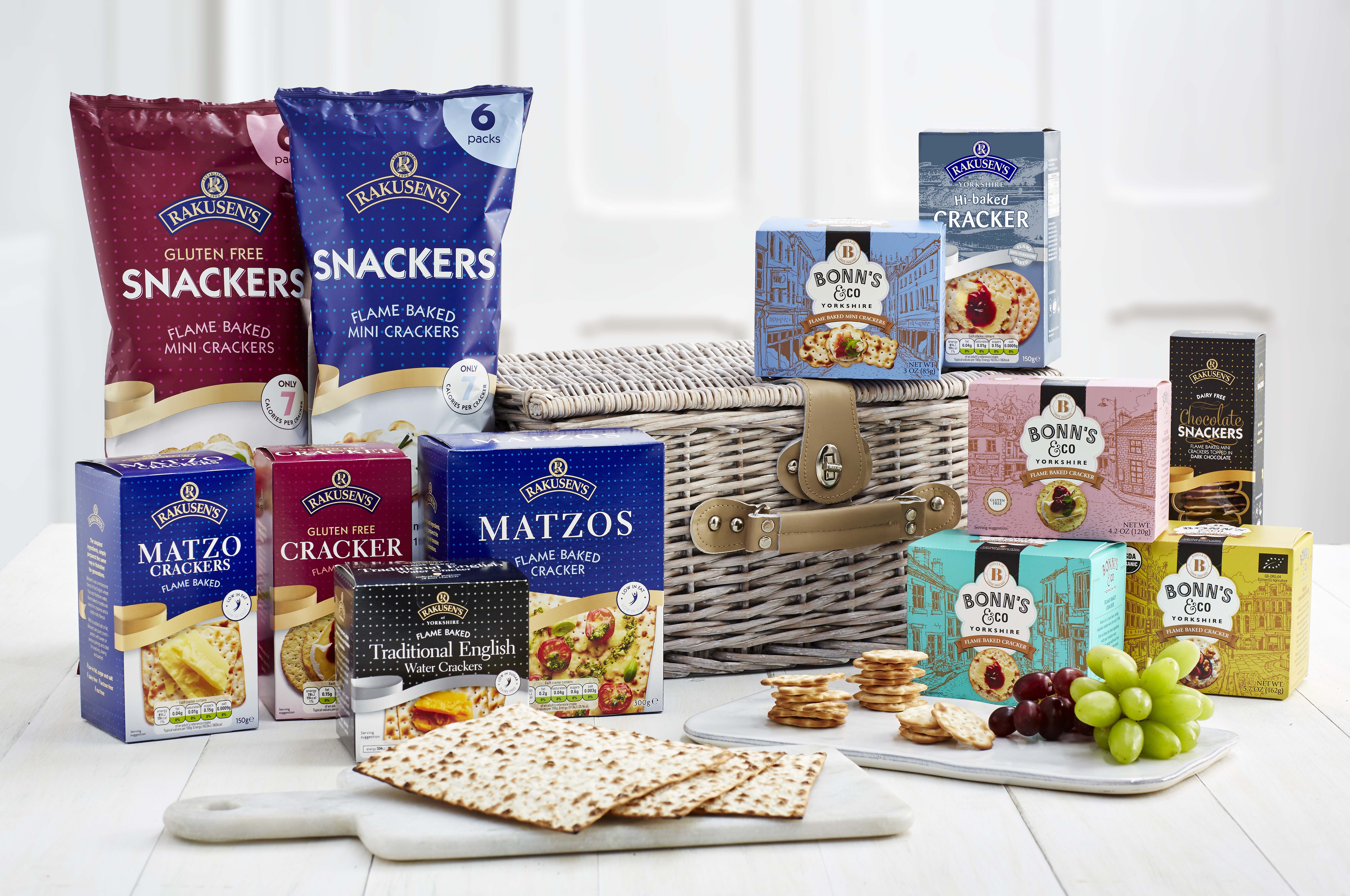
Expanding Communications Capability with BNL (UK) Ltd
Professor Ben Whiteside, Head of the Centre for Polymer Micro and Nano Technology in the Faculty of Engineering, undertook a research project with BNL Bearings to develop polymer based bearings for the automotive sector.
BNL Bearings, who strive to be a world class market leader in polymer bearing solutions, worked with Ben on a KTP to investigate early indications of bearing wear properties with specific material types before committing to lengthy life cycle studies. Ben and the company recruited an Associate to manage the project. The findings indicate that there has been a substantial uplift in dynamic load rating capabilities of certain materials for bearings. These rolling element bearings perform above 90 degrees centigrade and exhibit low thermal expansion for under bonnet applications. Two working prototypes were developed along with a design calculator tool which is now fully deployed in BNL’s new Product Development Department.
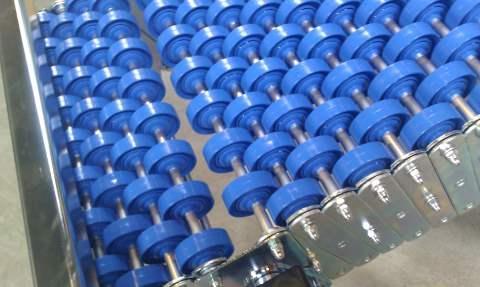
The KTP has helped Ben and his team understand the critical elements required for strong industry partnerships. The outcomes have been incorporated into teaching activities and modules for the next academic year. The KTP has also given final year students interesting topic areas for their projects, with one student delivering a project for the company and gaining a first class mark. Further student placements are being explored by the company.
As part of the KTP, the Associate, Karolis undertook a number of industry standard qualifications, gained membership to professional institutes and presented the project at various professional events. He has since secured employment at the company as an R&D Engineer.
BNL have already been approached by customers for the new range of products with interest expected to dramatically increase when more successful outcomes are available. They have also saved time on each project using the new design calculator tool.
This KTP received a 'very good' grading from Innovate UK.
Expanding Communications Capability with Seven Technologies Group Ltd
Seven Technologies Group Ltd worked with the faculty of Engineering and Informatics on this Knowledge Transfer Partnership (KTP). The collaboration aimed to expand the capability of specialist communication systems and develop, implement and test new energy-efficient coding, signal processing methods and hardware innovations, for existing and new commercial products within a short timescale.
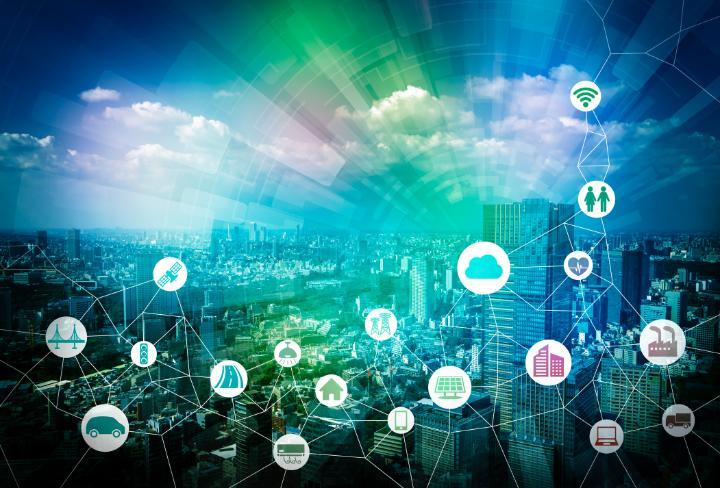
Project outcomes
The project laid the foundations for a future generation of tracking systems for the company and very positive financial projections from increased sales. It opened up opportunities for new teaching materials, student projects and research theses and 22 academic papers were written as a result. Innovate UK graded it outstanding and both associates are now employed in the company.
The project has been very successful from both the company’s perspective and the University’s, bringing tangible results in terms of product designs and ideas, and in transferring expertise to engineers within the company.
“The KTP exceeded our expectations in terms of quality and quantity of output as well as creating strong links with our academic partners. It has delivered significant value for money and laid the foundations for the revolution of our core technology to meet the challenges of the future." Simon Marker, Research and Development Director at Seven Technologies.
Business benefits
The company received great support from the University, enhancing their knowledge base throughout the development cycle of these research areas, but also practically, including use of the University’s measurement facility for evaluating operation performance of the proposed diversity antenna system. There were many important and insightful discussions and suggestions to the technical difficulties encountered, with a relaxed yet focussed atmosphere prevailing throughout.
The design of a novel antenna array system to include the compact small antenna transmitter has helped Seven Technologies realise their future antenna design transceivers, improving their position with a competitive market.
New software to introduce narrow band and wideband signal processing methods has enabled them to identify the ‘angle of arrival’ (AOA) of radio signals to support radio-location and tracking needs. The company has improved their engineers’ knowledge of how their existing systems function.
Design and implementation decisions are now more informed and with a sound technical base, placing the company in a better position to develop the next generation of RF based tracking systems.
Improving Polymer Processing Techniques CRP Ltd
CRP Ltd worked with the University of Bradford’s Faculty of Engineering and Informatics on this Knowledge Transfer Partnership (KTP). The focus of the project was the polymer perfluoroalkoxy (PFA).
PFA is a melt processable fluoropolymer, principally comprising carbon and fluorine atoms in a molecular chain. This structure gives the material its exceptional corrosion resisting properties, but also results in its challenging processing characteristics.
The project aim was to gain an enhanced understanding of key process variables and to allow increasingly large and complex products to be manufactured.
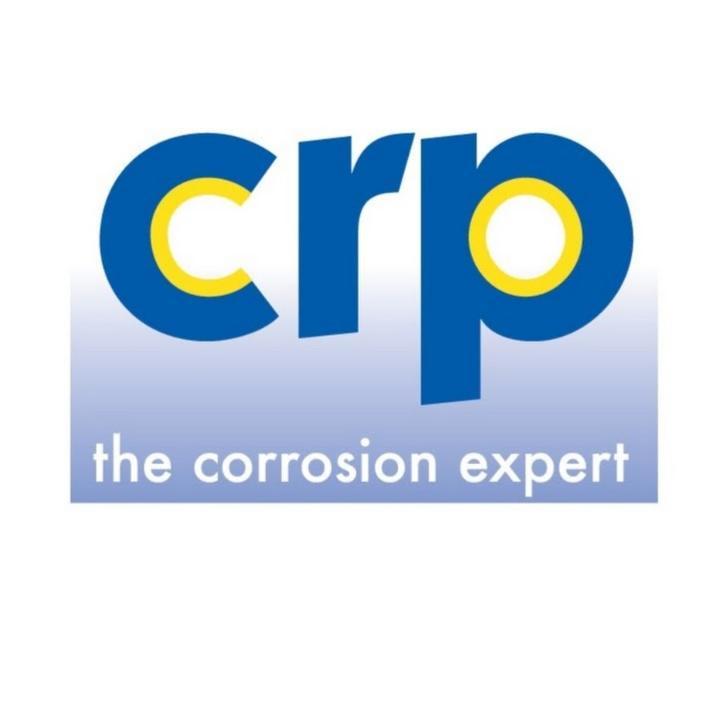
Project Outcomes
The pot moulding process for PFA was instrumented so that data could be recorded to understand why moulded parts were failing. This data informed modifications in the moulding process to improve product flow and ensure the parts created passed product testing standards. Material flow characterisation and flow processes were documented for the revised process and shared with staff, leading to much greater knowledge of PFA processing techniques.
“Part of the company’s strategy has been to develop its PFA moulding capability to allow it to manufacture both larger and more complex components. The KTP fits directly into this strategic aim.”
David MacGregor, Engineering Manager, CRP Ltd.
Visit the Centre for Polymer Micro and Nano Technology.
Business Benefits
The KTP has enhanced CRP’s abilities in PFA moulding to allow it to mould both larger and more complex components, making it more competitive in an international market.
The company now have a greater understanding of PFA processing, the width of PFA’s processing envelope, how long it takes to heat PFA prior to production, and how to melt large quantities of the polymer.
Nutritious gains of in-house granulation with Principle Healthcare Limited
Principle Healthcare worked with the Centre for Pharmaceutical Engineering Sciences to research the option of developing in-house granulation technology for their nutritional supplements.
The Company purchased pre-granulated materials for their nutritional vitamins, minerals and supplements and wanted to explore the benefits of granulating high volumes of their own materials instead, whilst still maintaining a quality product.
The Associate and academics carried out detailed research into the materials, regulations, and processes connected to the Company’s supplements and developed a Material Product Property Performance (MPPP) database to predict the quality of granulating the materials and the re-formulation required. They also investigated the changes, risks and costs needed to convert to in-house granulation.
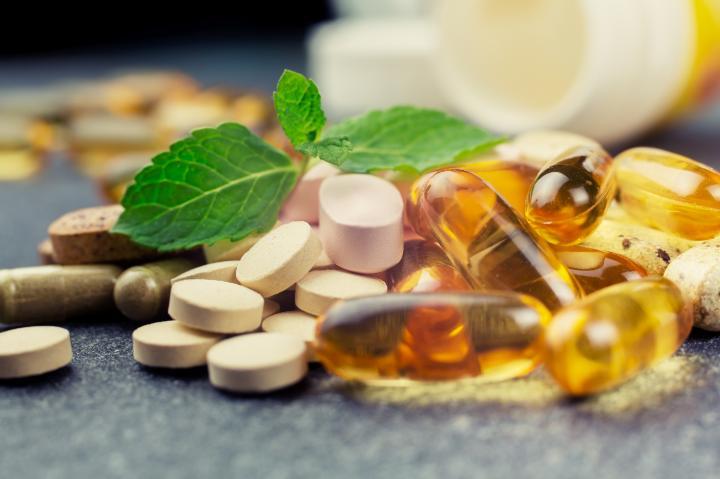
Project outcomes
Positive granulation trials using the University’s equipment led the Company to invest in a high shear granulator. The machine enables the company to granulate raw materials themselves rather than buying them in pre-granulated form. Buying raw materials, rather than pre-granulated, has given them access to a wider range of suppliers.
The hot melt granulator can also be used to blend ingredients. This has increased the Company’s blending capacity by 12%.
“The KTP project has exceeded our expectations. It has helped increase engagement with open innovation from all areas of the business and embed it into our company’s core values. We have a good relationship with the University of Bradford and will work on future collaborative projects together.” Clare Campbell, Group Quality Director, Principle Healthcare Limited.
Principle Healthcare Limited is one of Europe’s leading manufacturers of nutritional supplements: formulating, manufacturing and packaging vitamins, minerals and supplements in a variety of formats.
The Centre for Pharmaceutical Engineering Sciences partnered with Principle Healthcare.
Business benefits
Principle Healthcare now has the knowledge and ability to granulate raw materials with revised regulations and formulations to support it. They have cross-functional teams trained to use the new manufacturing process and a training package ready for new users. The new manufacturing facility brings with it the capacity to compete in new product categories, enter new markets, and increase international export.
The KTP has also inspired a new culture of open innovation, idea generation, and cross disciplinary working. To underpin this, the KTP Associate, Suyog Aher, has secured a permanent position in the company to develop and implement innovative manufacturing and testing technology.
The MPPP database, developed as part of the trial, has strengthened the Company’s research base, leading to further opportunities for collaborative research grant applications.
Digital data transforming business intelligence with Incommunities Group Ltd
Incommunities Group worked with the University of Bradford to increase efficiency and effectiveness in a difficult climate of government cuts to social housing by creating a decision support system (DSS) that Incommunities could use to make better business decisions on customers and stock performance. Once the project was underway and data had been analysed, the project was widened to include data quality to address gaps in the data gathered.
-720x478.jpg)
Project outcomes
The project developed a bespoke financial framework and established a Business Intelligence Team to implement the framework and integrate the DSS into the organisation. The Business Intelligence Team were also given the remit of ensuring the right kind of data is collected.
The KTP Associate is now employed permanently in the company and a strong collaborative partnership between both organisations has been developed.
“The real benefit of the KTP is not only in the outputs; it is that the organisations eyes are opened to new possibilities. By taking time to reflect and consider how to take the business forward, the KTP brought invaluable insight that resulted in transformational change.”
Dave Dickens, Director of Income and Customer Services, Incommunities.
Project benefits
The project occurred at a particularly challenging time for Incommunities, who were experiencing significant funding cuts and whose customers were faced with rising costs and reduced income. However, during the life of the KTP the company achieved a £5m increase in turnover and £150k savings in fencing and fuel supplies.
The creation of a financial framework aided the development of an organisational roadmap to 2025 and contributed to a detailed analysis of market position and organisational performance. Clarity over marketing positioning helped inform decisions such as acquiring or releasing assets and expanding the geographical area of operation.
The companywide sustainability framework influenced a change in culture that led to them achieving their highest regulatory outcome judgements. Incommunities next steps are to expand the scope of the DSS to include energy efficiency and develop a training programme that will further embed the new sustainability strategy into its culture so staff can advise customers on energy efficiency and other money saving strategies.
Engineering Technology for New Markets with Norgren Limited
Norgren Ltd worked with the University of Bradford's Faculty of Engineering and Informatics on this Knowledge Transfer Partnership (KTP). The collaboration aimed to provide an understanding of the detailed mechanical, fluid and material principles of Norgren's existing Current to Pressure (I/P) converter leading to the design of a new generation of products.
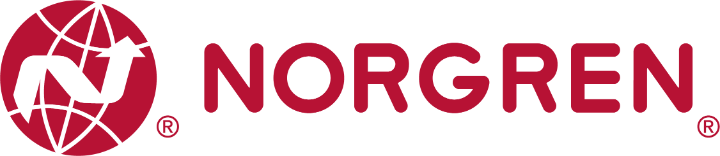
Project outcomes
The project research and design to optimise existing products resulted in invention and patent application for a new technology and new products created a presence in existing markets, new market opportunities and a stronger capability in the energy sector. Further KTPs are planned with other parts of the Norgren Group.
“The KTP has been an excellent partnership, allowing us to apply expert skills to solve real world problems. The structure and support
provided by the KTP programme was a model for future projects." Dave Thompson, Technical Manager, Norgren Leeds.
Project benefits
This collaboration has generated a significant number of benefits for Norgren. The existing I/P convertor function was simulated to study its normal operations allowing the effects of changes in geometry, temperature, current or material properties to be predicted.
A mathematical expression was created so the effect of a design change could be predicted with ease. Using the mathematical equation, a new counterbalanced beam was designed which removed problems and reduced the effects of vibration. A patent application was submitted for new beam invention.
This work has addressed the need for a more stable and low power current to pressure convertor, enabled the core technology to be applied to a specific new product, and opened up further opportunities to include this technology within new customer’s devices.
State of the art micro products with Precision Polymer Engineering
The partnership between PPE and the University of Bradford was established to develop a state of the art production facility for the manufacture of micro-sized products in a broad range of elastomer materials. The objective of the project was to create an industry leading capability for the provision of micro parts in critical applications.
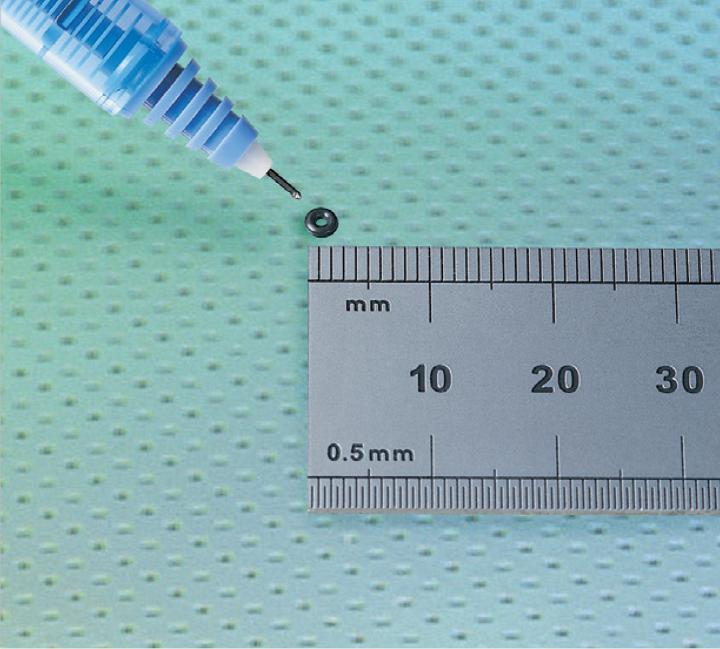
Project Outcomes
The overriding objective was a consistent and repeatable process, providing the highest quality micro-parts to address sealing requirements for industries such as micro-fluidics. High quality micro-elastomer parts can then be used to replace PTFE and PEEK materials to provide a more robust sealing solution.
The University of Bradford in collaboration with PPE have published a research paper defining the development activity of the project. The knowledge gained through the project has created innovative techniques for the processing of elastomer materials which was previously impossible. The Knowledge Transfer Partnership (KTP) has provided opportunities for other final year students with associated projects.
“It’s been a good experience with opportunities to grow in niche markets and increase sales and profits. The University have been excellent.
The selection of the associate and a good relationship with the University are very important.“ Paul Haworth, Global Product Development Manager, Precision Polymer Engineering Ltd.
Business benefits
Precision Polymer Engineering’s employees have gained new micro-moulding technology and software knowledge and experience in related magnification, measurement and robotic techniques. As a result of the project the company are investing in the development of this knowledge as part of their strategic plan.
The Associate (graduate) has become a permanent employee in the company and is responsible for setting up a micro manufacturing cell.
By establishing a flexible state of the art production facility for manufacturing micro-sized elastomer material products, the company have developed a niche customer offering in a difficult market. This is resulting in a more competitive offering, opening up new growth markets, and cementing their position as the leading provider of sealing component solutions in the future.
Reducing Irritants in Skin Products with RB Healthcare Ltd
This KTP supported RB Healthcare Ltd to reduce the irritancy potential of their skin product formulation by developing a new in vitro (test-tube experiment) modelling strategy to understand how topical formulations can impact on healthy and compromised skin.
Business benefits
The project aligned perfectly with a recent shift in focus to the Health and Hygiene pillars, which are 2 of RB’s strategic pillars. RB aimed to improve its capabilities by increasing speed and lowering costs for in vitro skin irritancy testing methods. The KTP helped the business develop an understanding of the available capabilities and methods that they can apply to future new developments in those fields.
The KTP resulted in RB developing Standard Operating procedures (SOP’s) that will inform future in vitro testing techniques by guiding decisions on appropriate tests for the product and properties being studied. This knowledge will help RB reduce errors, chose appropriate business partners, and interpret test results to contribute to remaining at the forefront of a rapidly changing landscape of in vitro testing.
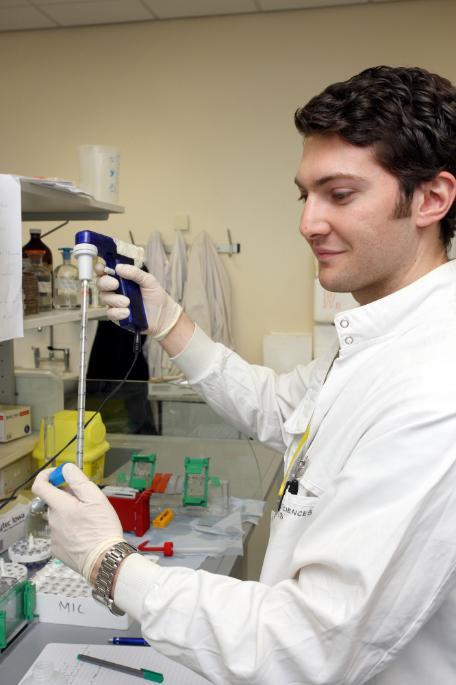
Project outcomes
The partnership provided the company with the opportunity to acquire new skills and techniques in skin and hair-associated product development which resulted in a competitive advantage in the personal care field. They identified gaps and strategies relating to decision modelling methods and developed Standard Operating Procedures (SOPs) to guide future in vitro irritancy testing.
The University were able to gain new knowledge in human 3D epidermis, a greater understanding of toxicology issues relating to personal care products and ingredient insight for skin products formulation. Professor Des Tobin and colleagues are continuing to develop research relationships with the company.
“The KTP project brought the business into contact with a world class skin expert, Professor Des Tobin. His valuable knowledge has helped guide the company’s developments within and outside the scope of the project.” Scott Seville, Technology and Innovation Manager – Germ Protection and Personal Care RB Healthcare (UK) Ltd.
Improving Customer Experience through E-Strategy with Sovereign Health Care
Sovereign Health Care worked with the Faculty of Engineering and Informatics on this Knowledge Transfer Partnership (KTP). The collaboration aimed to develop and embed an organisation wide e-strategy to process healthcare claims, manage healthcare policies and communicate with customers and employees electronically.
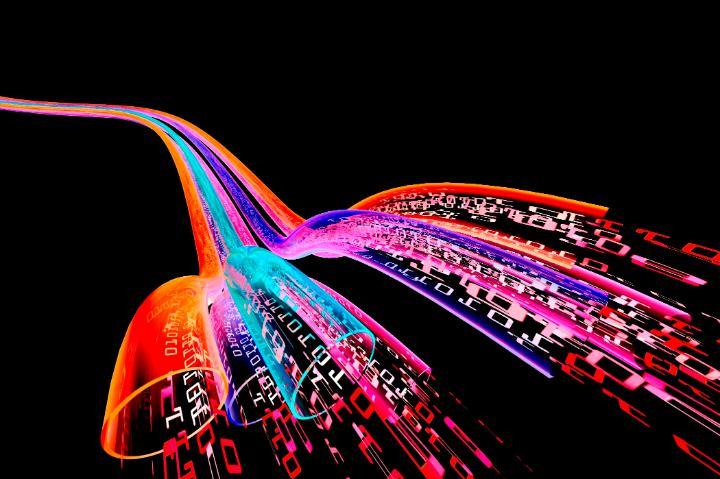
Project outcomes
For Sovereign Health Care, the project created a better customer experience and more competitive new customer offering through development of e-systems, and generated staff efficiencies and improved internal communication as a result of the introduction of electronic claims processing and updated intranet.
The academics gained an improved business profile, knowledge and skills, enriched their teaching and created a new accredited module.
“To get the best possible outcome from your KTP, involve as many stakeholders at the outset and collaborate with colleagues wherever possible to get maximum buy in.” Russ Piper, Chief Executive, Sovereign Health Care.
Business benefits
This collaboration has achieved a significant amount towards its original aim. An e-strategy was created following in-depth research around e-capabilities, customer needs, and competitor activity. Significant work has been done on staff development and system design and content for e-claims processing and an e-portal.
A change in regulatory rules prompted a review of the company’s IT systems and highlighted potential risks. This resulted in Sovereign Health Care having to re-visit the e-strategy part way through the project to align it to a new IT system. When the new e-claims processing system is implemented it will simplify the claims cycle for the company and the customer. The Associate remained with the company to migrate the work done into the new IT system.
Developing digital capability and anticipating consumer trends through this collaboration will impact positively on company performance for Sovereign Health Care’s next generation of customers. The use of digital platforms such as “direct response television”, the red button, smart phone applications and multimedia technology are significant areas the company intends to explore in the future.